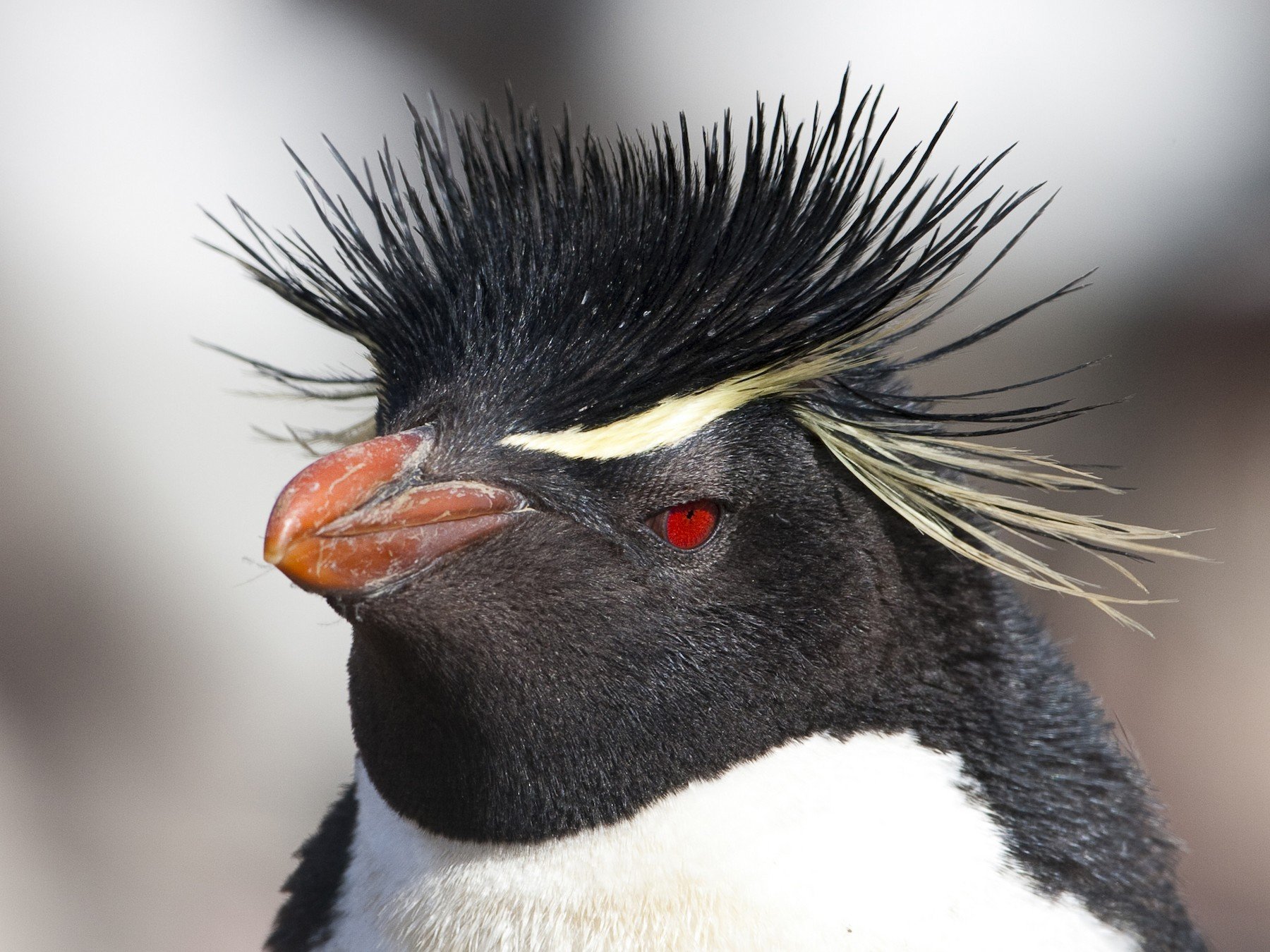
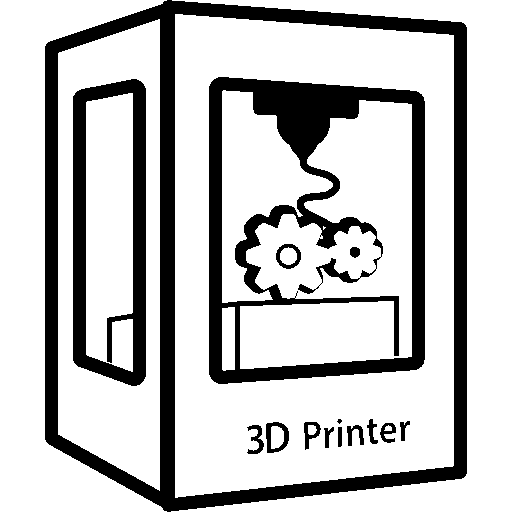
Your slicer should also be able to compensate for this already.
PLA only shrinks about 0.3% which is negligible unless you are designing with super tight clearances. A 6mm hole, for instance, will be out 0.018mm which is probably scraping against the XY resolution limits of most consumer 3D printers anyhow.
Other materials can definitely shrink more. ABS is harder to manage than PLA, but for instance Nylon/PA’s shrink rate is comparatively immense – around 2%. The various engineering polymers that are filled with something like carbon or glass fibers actually tend to shrink less than their raw counterparts.
My Qidi has a heated chamber and can allegedly do it stock, and I’ve had an unopened spool of pure Nylon sitting in the printer cabinet for over a year.
But I’m chicken.
If your nozzle can withstand it, glass filled is way easier to print.